Some Known Factual Statements About Alcast Company
Table of ContentsIndicators on Alcast Company You Need To KnowAlcast Company Things To Know Before You Get ThisAlcast Company Things To Know Before You Get ThisLittle Known Facts About Alcast Company.3 Simple Techniques For Alcast CompanyAlcast Company Things To Know Before You Get This
Chemical Comparison of Cast Light weight aluminum Alloys Silicon advertises castability by decreasing the alloy's melting temperature level and improving fluidness during casting. Additionally, silicon adds to the alloy's stamina and put on resistance, making it valuable in applications where toughness is important, such as vehicle components and engine parts.It also boosts the machinability of the alloy, making it easier to process into completed items. In this way, iron adds to the overall workability of aluminum alloys.
Manganese adds to the strength of aluminum alloys and boosts workability (aluminum foundry). It is typically made use of in wrought light weight aluminum products like sheets, extrusions, and profiles. The visibility of manganese help in the alloy's formability and resistance to breaking during manufacture processes. Magnesium is a light-weight component that provides stamina and impact resistance to light weight aluminum alloys.
Not known Incorrect Statements About Alcast Company
Zinc boosts the castability of light weight aluminum alloys and aids regulate the solidification process during spreading. It boosts the alloy's strength and hardness.
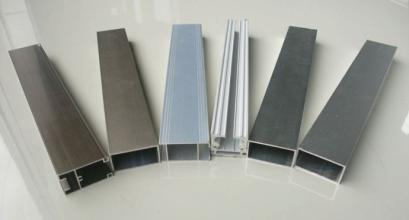
The key thermal conductivity, tensile toughness, yield stamina, and prolongation vary. Select appropriate raw products according to the performance of the target item produced. Amongst the above alloys, A356 has the highest possible thermal conductivity, and A380 and ADC12 have the lowest. The tensile limit is the contrary. A360 has the very best return strength and the highest elongation rate.
Some Of Alcast Company

In accuracy spreading, 6063 is fit for applications where intricate geometries and high-quality surface finishes are extremely important. Examples consist of telecommunication enclosures, where the alloy's superior formability permits sleek and cosmetically pleasing layouts while maintaining architectural stability. In the Illumination Solutions market, precision-cast 6063 parts produce sophisticated and reliable lighting fixtures that call for intricate shapes and excellent thermal efficiency.
The A360 shows premium prolongation, making it perfect for facility and thin-walled parts. In precision spreading applications, A360 is fit for industries such as Customer Electronic Devices, Telecommunication, and Power Devices.
Alcast Company - Truths
Its distinct buildings make A360 a beneficial option for accuracy spreading in these markets, enhancing product longevity and quality. Casting Foundry. Aluminum alloy 380, or A380, is a widely utilized spreading alloy with several distinct features.
In precision casting, aluminum 413 shines in the Customer Electronics and Power Devices sectors. This alloy's exceptional rust resistance makes it a superb option for outdoor applications, making certain durable, durable products in the discussed industries.
Indicators on Alcast Company You Need To Know
The light weight aluminum alloy you pick will significantly influence both the casting procedure and the homes of the last product. Because of this, you have to make your decision very carefully and take an enlightened method.
Determining the most appropriate light weight aluminum alloy for your application will certainly mean considering a vast range of qualities. The initial classification addresses alloy attributes that influence the production process.
The Facts About Alcast Company Uncovered
The alloy you choose for die casting directly influences numerous aspects of the casting process, like how easy the alloy is to work with and if it is vulnerable to casting flaws. Warm breaking, also called solidification breaking, is a common die spreading defect for light weight aluminum alloys that can cause internal or surface-level splits or splits.
Particular aluminum alloys are a lot more susceptible to hot fracturing than others, and your selection should consider this. It can damage both the actors and the die, so you must look for alloys with high anti-soldering homes.
Rust resistance, which is already a significant attribute of aluminum, can differ substantially from alloy to alloy and is an essential characteristic to take into consideration depending upon the environmental conditions your item will be subjected to (aluminum foundry). Put on resistance is one more property frequently sought in light weight aluminum explanation products and can set apart some alloys